There are various legal industry compliance requirements for a manufacturing business. These businesses also face a variety of risks and compliance issues in manufacturing and obtain certification of compliance in manufacturing. Before starting a manufacturing business, you will need to obtain licenses and permits from various levels of government, including at the federal, state, and local levels. Commercial lawyers can assist you in defining and achieving your goals while maximizing your rights and minimizing risks.
What Is Manufacturing Regulatory Compliance?
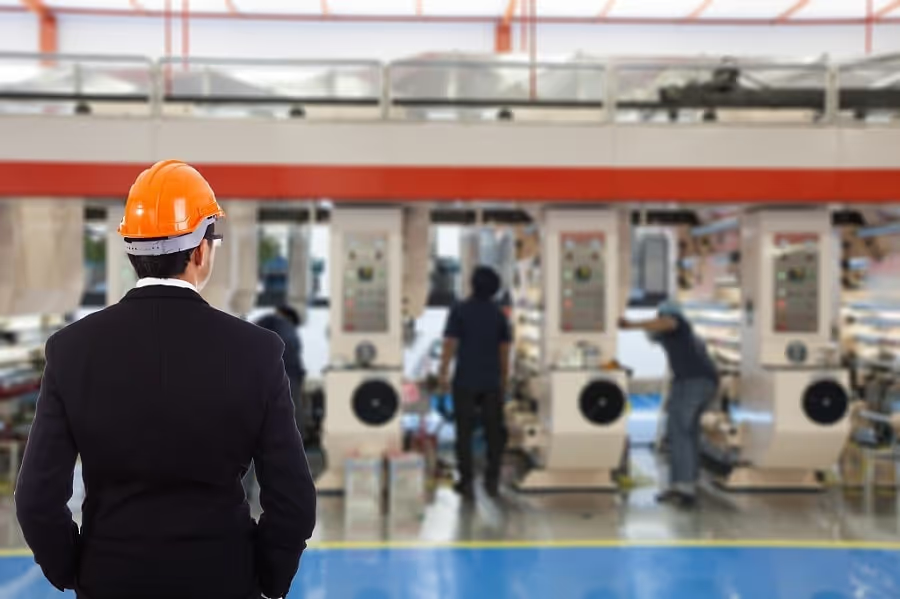
Manufacturing compliance includes a broad range of regulatory compliance procedures that protect manufacturing companies and consumers from the risks of compliance breaches. They set out the requirements for businesses to legally bring their manufactured products to market. Various production compliance areas can come into play in the process of bringing a product to market. Areas include federal and state laws covering product safety, data protection, export controls, employment law, and fair competition, as well as international laws.
Any manufacturing product that is regulated by the FDA will be subject to additional regulatory compliance requirements, including under Title 21 of the Code of Federal Regulations Part 11 and Part 820. Part 11 obligates pharmaceutical manufacturers, medical device companies, biotech, and biologics development companies to implement specific controls, including audits, electronic signatures, and other forms of documentation requirements. If a business manufactures an FDA-regulated product, it is important to verify any additional regulatory or compliance obligations that may apply.
Why Is Manufacturing Compliance Important?
Why is legal compliance important? If a business has compliance issues or risks in manufacturing, the stakes can be high. Failure to comply with manufacturing compliance requirements poses reputational and financial risks. In addition, it exposes your business to legal risks and production/manufacturing delays.
What Legal Requirements Are Needed to Start a Business?
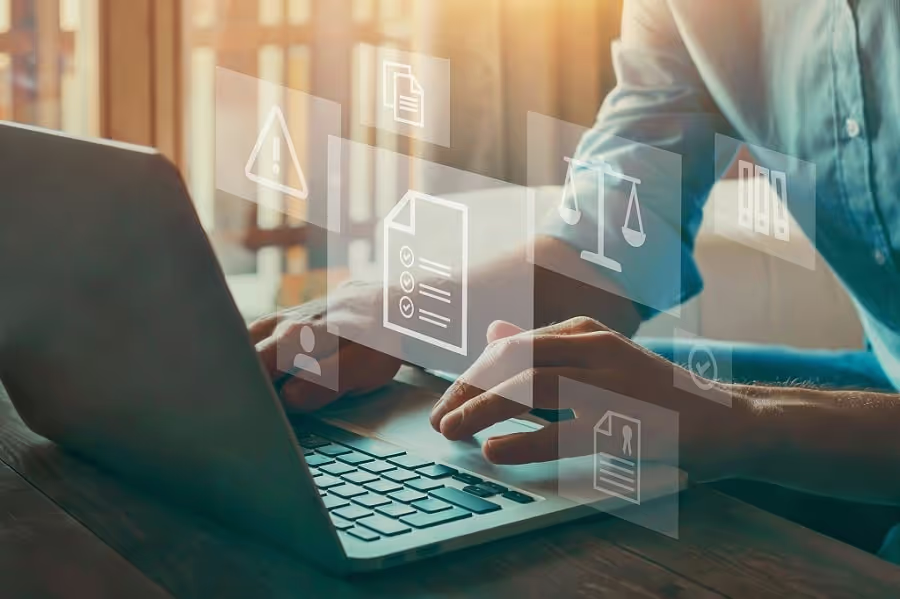
There are various statutory and regulatory requirements to start manufacturing companies. You will need to conduct a risk assessment and design manufacturing company policies to establish and maintain compliance.
The licenses required for manufacturing business and manufacturing permits include:
- EIN or tax identification number from the federal government in addition to a similar tax ID from the business’s state of operation;
- A basic license for the operation of the business, obtained from the city or county where the manufacturing business will be located;
- Land use and zoning permits covering the full breadth of your company’s operations;
- Sales tax license permitting the sale of any goods manufactured by your company;
- A health department permit if your company is manufacturing any food or other regulated products;
- Building permits;
- A special license is required for manufacturing businesses if your company produces drugs, tobacco, alcohol, or firearms. To determine which permits are required, contact the U.S. Food and Drug Administration (“FDA”) or the U.S. Bureau of Alcohol, Tobacco, and Firearms.
You should contact a commercial attorney to determine if there are any additional licenses required for your company.
What Is a Certificate of Compliance in Manufacturing?
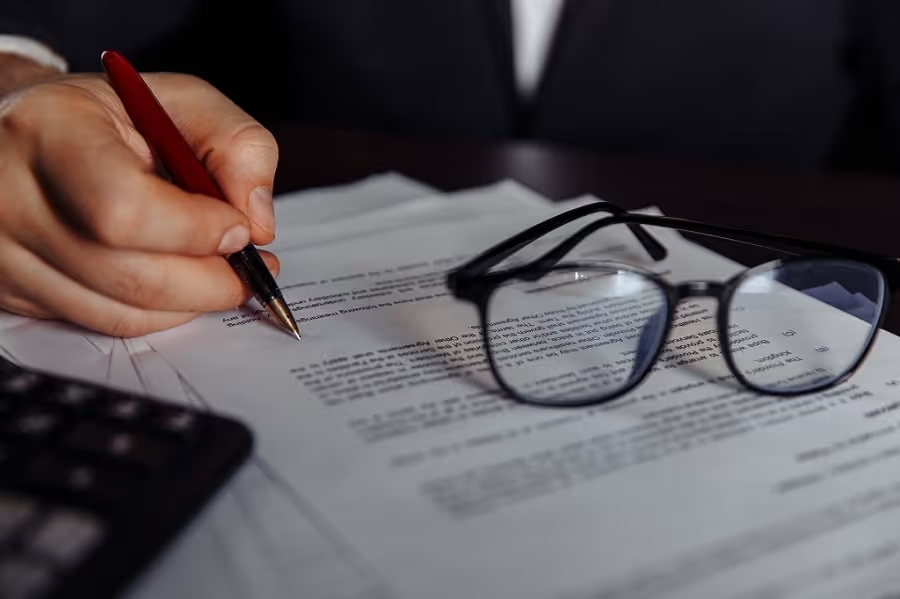
A Certificate of Compliance (CoC) is issued by the manufacturer. This certificate attests that the manufacturer met all the regulations relevant to the particular product. It also verifies that the company sought and obtained any mandatory third-party testing or reviews of its products and processes.
Finally, it confirms that the goods met the required specifications. For example, when manufacturing companies produce electrical appliances, they must meet industry standards, abide by state and federal consumer protection laws, and comply with industry testing requirements.
Different Types of Compliance and Manufacturing Certificates
Various types of compliance are of particular importance to manufacturers. These include:
- HIPAA (Health Insurance Portability and Accountability Act of 1996): this is a federal law requiring standardization of mechanisms for protecting sensitive patient health information from being disclosed without explicit consent from the patient;
- PCI-DSS (Payment Card Industry Data Security Standard): this regulation applies to companies that handle major branded credit cards and is designed to protect the cardholder’s data that is shared, processed, or stored during a transaction;
- SOC 2 (Systems and Organization Controls): this describes a suite of reports that are reported during an audit that is intended to be used to validate internal compliance controls;
- SOX (Sarbanes Oxley Act of 2002): this Act outlines requirements for all private and public companies that handle financial data;
- ISO (International Organization of Standardization): the ISO is an international body that sets industry standards;
- GDPR (General Data Protection Regulation): this governs the EU General Data Protection Regulation replacing the EU Data Protection Directive and its local implementing laws. The GDPR requires companies that process personally identifiable data in the EU to demonstrate compliance with its requirements.
Any manufacturing business with international operations should also be aware of key international industry standards for compliance issued by the International Organization for Standardization (“ISO”) including:
- ISO 50001 certification – Energy Management;
- ISO 14000 certification – Environmental Management Systems;
- ISO 22000 certification – Food Safety Management;
- ISO 45001 certification – Occupational Health and Safety Management Systems;
- ISO 27001 certification – Information Security Management;
- ISO 9000 certification – Quality Management;
- ISO 13845 certification – Plastics Piping Systems;
- International Electrotechnical Commission (IEC) 61215 certification – Terrestrial Photovoltaic (PV) Modules;
- IEC 61646 certification – Thin-Film PV Modules.
This international standards organization is recognized for its comprehensive compliance requirements for manufacturing companies.
How to Get a Certificate of Manufacturing Compliance
To obtain ISO certification and statutory compliance for the manufacturing industry, your business must find an accredited certification body that uses the relevant Committee on Conformity Assessment (CASCO) standards.
Manufacturing Compliance: Checklist for Your Business
You will find many sources for developing a manufacturing compliance plan, ranging from OSHA to Underwriters Laboratories.
Some possible compliance measures include:
Safety
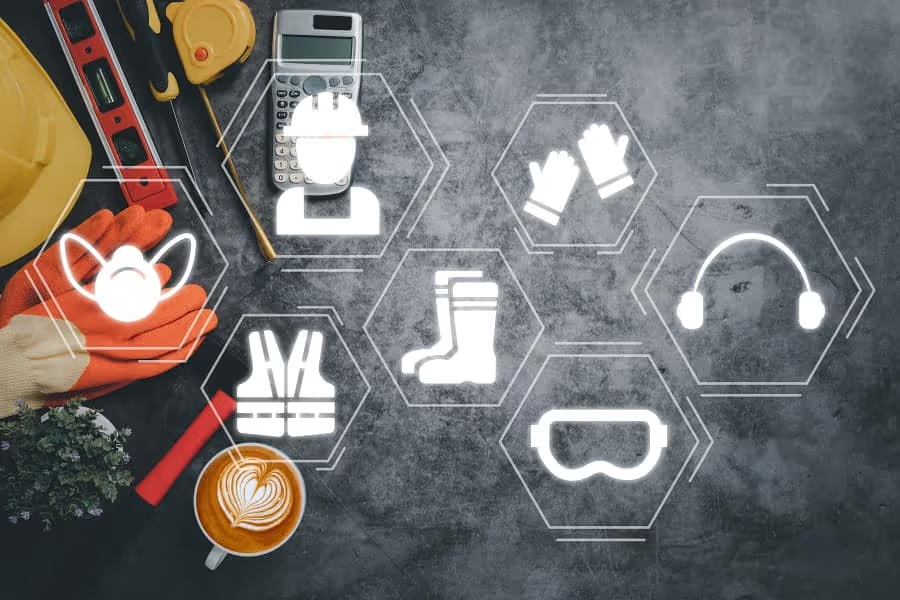
Has your business:
- Provided adequate safety equipment?
- Inspected machines to ensure guards are positioned and functioning correctly?
- Monitored worker compliance with safety procedures?
- Ensured workers dress safely?
- Provided operating safety equipment, including eye-wash stations and fire extinguishers?
You will often see these requirements from OSHA and your insurer.
Materials and Tools
Do workers have access to:
- The materials and tools necessary to meet specifications?
- Manufacturing procedures explaining the use of tools and materials?
- Functioning and well-maintained equipment?
You will typically find specifics regarding these requirements among your industry's standards.
Motions
Have you reviewed your worker processes to ensure:
- Efficiency?
- Uniformity?
- Ergonomics and minimization of repetition?
These requirements will often come from a review by efficiency and safety experts.
Workstation
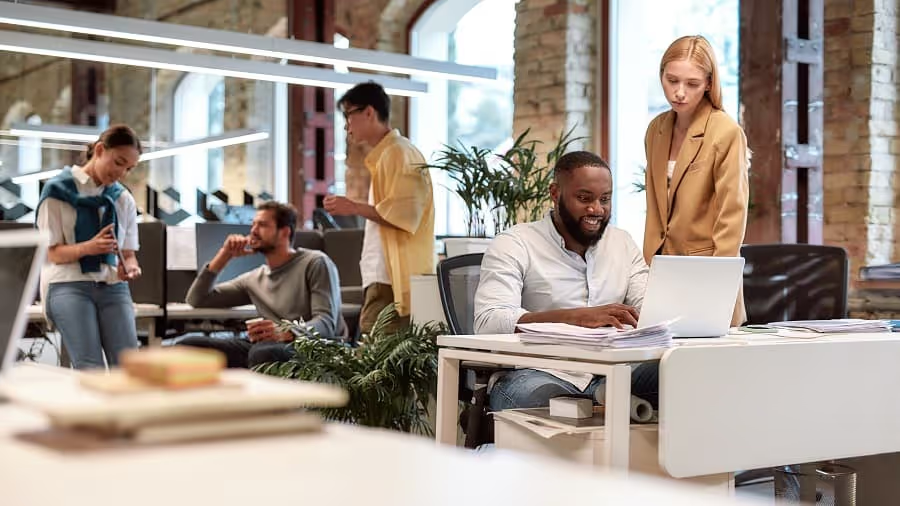
Have you reviewed your facility and its location for:
- Shipping and receiving efficiency?
- Safety?
- Adequacy for its tasks?
- Inspectability for compliance?
Industrial engineers and designers may review your manufacturing facilities for these measures before you begin implementing your manufacturing processes.
Reporting and Documentation
Does your business provide procedures for reporting and documenting:
- Employee concerns and complaints?
- Problems and inefficiencies in manufacturing processes?
- Improvements to training procedures?
- Steps taken in response to complaints, safety issues, and manufacturing inefficiencies?
Additionally, you should determine if all workers comply with the documented processes and have access to the most recent versions of them.
5 Steps to Implementing a Manufacturing Corporate Compliance Plan
When implementing a manufacturing corporate compliance plan, there are various steps to consider and take to meet manufacturing requirements and obtain a factory compliance certificate.
1. Research
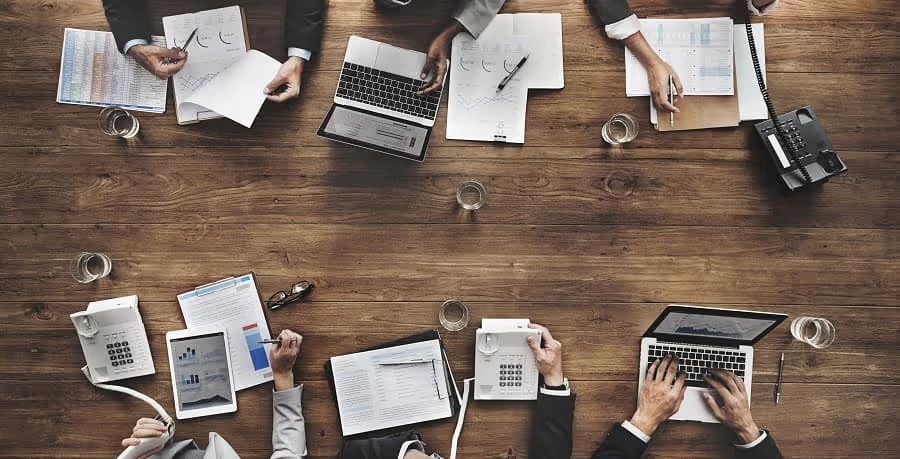
Your business should start by researching any regulatory requirements that apply to the product you are manufacturing. This research will focus on any state or country-specific regulations in addition to any additional compliance requirements imposed by federal agencies like the FDA.
2. Set Goals and Understand Risks
Next, business stakeholders should meet and discuss any perceived or known compliance risks that exist for the manufacturer. Stakeholders must set goals to address these deficiencies or create a stronger comprehensive compliance program and appoint a chief compliance officer to determine how to reach them. The business should focus on developing a robust compliance training program for employees.
3. Provide Manufacturing Compliance Training to Employees
After designing the compliance training program, the business should set aside time to conduct the training and answer any questions that may arise during that training. Ensuring that employees are aware of compliance procedures is vital to the effective functioning of a manufacturing compliance program.
4. Make Compliance an Ongoing Effort
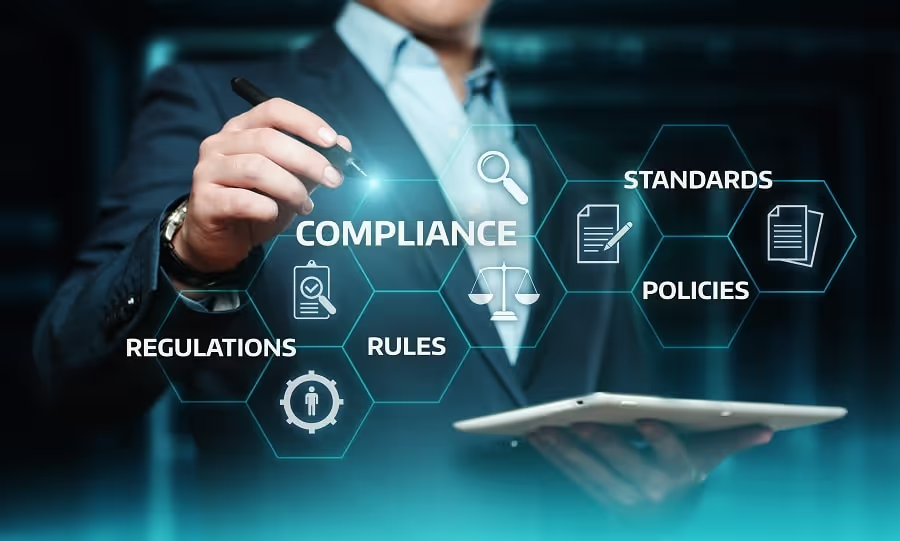
As part of this training, your business should emphasize the ongoing nature of compliance efforts. Namely, you should emphasize that compliance needs are constantly evolving and changing and that it is the role of each employee to remain diligent about compliance efforts, especially as your business continues to grow and scale.
5. Seek Legal Guidance
Many compliance efforts stem from legal or regulatory requirements. Even if you have a deep understanding of your industry and its processes, you might have never read the laws and regulations that apply to them.
Hiring a business formation lawyer will provide the peace of mind that your compliance plan meets not only the standards expected of manufacturing organizations but also the regulations about your type of products and services.
6. Create a Strategy for Non-Compliance
You must plan for something going wrong. You might receive substandard materials or a machine might get miscalibrated. This is why it's important to have a strategy in place to:
- Inform regulators
- Determine whether to recall products
- Correct the problem
Without this plan, your company's mistake might get compounded, particularly if it looks like someone tried to cover it up.
Benefits of Complying with Legal Requirements for Manufacturing Business
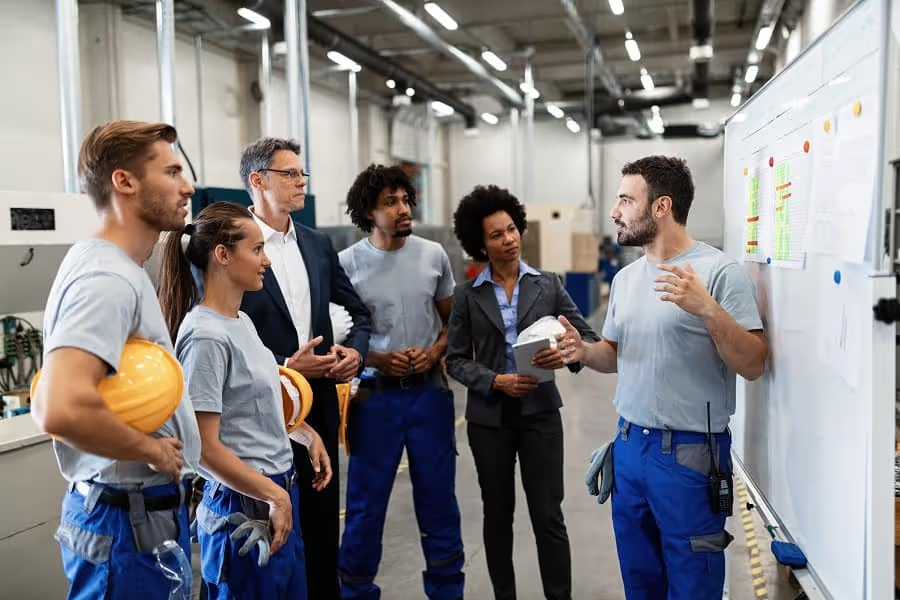
There are several benefits to developing a robust manufacturing compliance program.
To name a few:
- Reduced risk to the business, including to both employees and customers;
- Efficient communication within the business because employees are aware of compliance requirements and issues and are encouraged to flag issues with management and fellow workers;
- Reduced financial cost of regulatory violations or delays in getting your product to market;
- Minimizing harm to consumers.
As you approach your planning, keep in mind that compliance comes with lower legal fees and fewer reputational risks than trying to fix a problem after compliance failures.
Secure Your Manufacturing Compliance Certificate with Sequoia Legal Today
At Sequoia Legal, we know that complying with the different regulations and standards required to start and operate a manufacturing business can be burdensome. We are here to help you navigate these complicated compliance requirements so that you can focus on growing your business.
For more information, contact our legal team today!